When it comes to ensuring consistency in applying adhesives to products like cardboard boxes for diapers or bottles of wine, manufacturers often find themselves in sticky situations. An inability to see how much glue is dispensed and exactly where it was dispensed leaves them at risk of the packing failing during shipping.
For box sealing and other adhesive applications where the glue is dispensed inside machines, thermal imaging can help factory teams see what was previously impossible. By providing visibility and inspecting the glue applications as they happen, inline inspection solutions can alert operators to issues as they occur – avoiding issues and optimizing adhesive volumes.
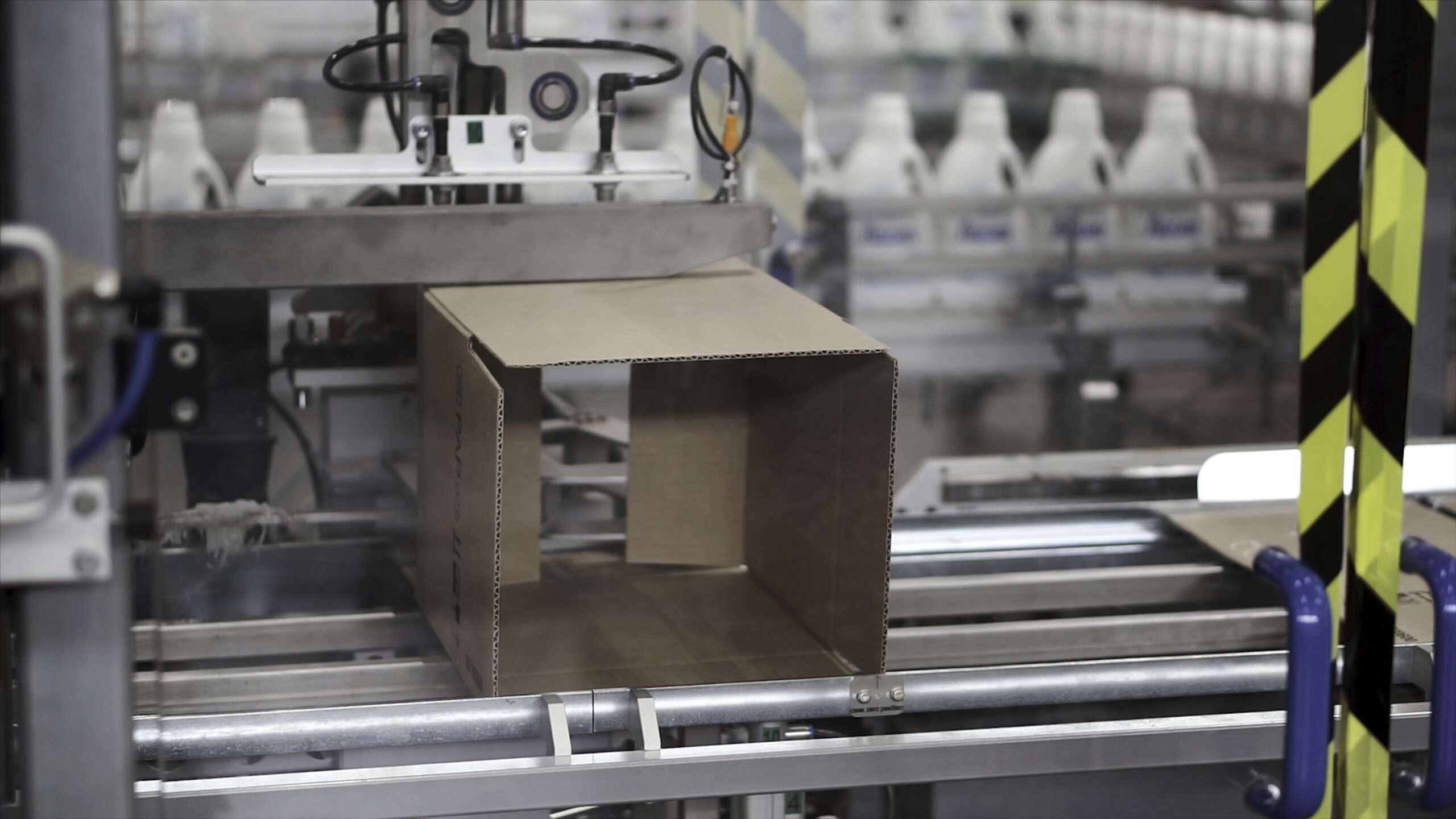
Cardboard box sealing machines allow to high volume packing. But monitoring and inspecting the glue applied to the box can be challenging because operators can’t see it.
While some adhesive dispensers come with vision systems, not all are created equal – especially those that rely on optical cameras. If you are considering an upgrade to an existing solution or want to explore adding thermal inspection to your adhesives application, ensure you consider the following:
1. What Hardware Will Best Serve Your Needs
The types of issues that you need to detect determine the hardware you require. In most adhesive applications, our team finds thermal cameras generate the best image data to support inline inspections. As noted above, adhesive applications are thermal so viewing heat signatures massively aids in delivering accurate inline inspections. The growing number of thermal camera hardware providers in the market has brought down the costs of thermal camera sensors.
2. How Will the Inline Inspection Solution Integrate with Your Current Process
We mentioned integration above. Integrating your vision solution means the data generated will be immediately useful and provide the most comprehensive inspections. Historically vision solutions for inline inspections have been standalone and the data captured required some manual manipulation for the images to be used for automating inline inspections.
3. How Will You Manage & Maintain The Solution
Most manufacturing teams don’t have resident machine vision experts. You want a solution that your team can manage and be repeatable so you can achieve standardized, consistent inspections across your machines. You want to be able to take that initial solution design and repeat it on subsequent lines. You want intuitive software that makes training and managing inspection models easy. You want to facilitate sharing of analytics and insights that drive improvements across your operations – not just on one line.
4. What About Software
While selecting the best camera sensor is important, you should consider the software. Sure, we’re biased, but you want to be able to manage standardized solutions that deliver standardized inline inspections. And you want an integrated inline inspection solution – capturing data from your machines and even triggering automated actions. Managing the solution – from configuration and integration to inspection model creation and management – should be easy and provide standardized reporting and centralized management when multiple inspection solutions are deployed.
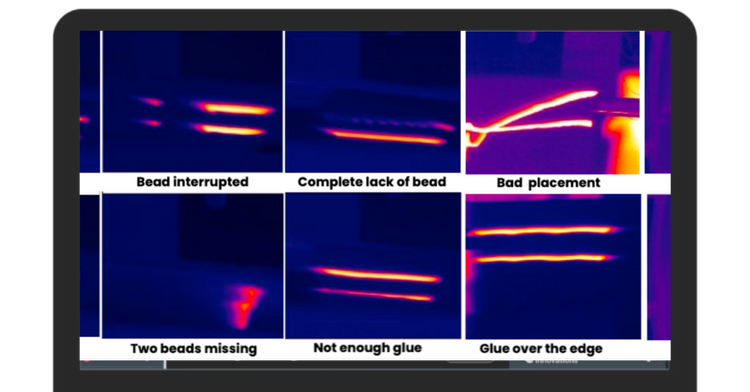
Inline inspections using thermal cameras capture of views and data required to train inspection models. Once deployed these models can detect issues and alert operators or automatically stop the process or remove the box from the line.
Our team is able to provide these tips and considerations based on our experience helping manufacturing teams design and deploy inline quality inspection solutions. Along with helping with camera and hardware selection and integration, the engineers on our Customer Solutions team use our OneView software to configure data flows and train factory teams to use it to review inspection records, easily apply labels and train and manage inspection models. And in those cases where multiple cameras are required, OneView imaging processing merges them to generate one inspection image.
If you find yourself in a sticky situation – unable to monitor your adhesive applications inline – talk to our team about deploying our inline inspection for adhesive solutions on your line. Click here.