Inline shell weld inspections allow factory teams to confirm the quality of welds during production. As automotive manufacturers strive for greater safety, efficiency, and quality control, ensuring the structural integrity of critical components like plastic gas tanks becomes increasingly essential. Plastic gas tanks must be resilient to handle pressure, temperature variations, and exposure to various environmental factors. Even a minor defect in the component or shell weld can lead to safety risks, environmental hazards, and costly recalls.
To meet these demands, manufacturers have historically relied on post-production, destructive testing methods that are both costly and wasteful. However, with thermal imaging and AI technology, manufacturers can perform inline, non-destructive inspections that ensure every weld meets stringent quality standards. Here, we explain our integrated solutions allow manufacturers to use thermal imaging and AI for real-time weld quality inspections for tank components and shell welds, ensuring precision, efficiency, and safety.
Inspecting Plastic Fuel Tank Component Welds with AI-Powered Thermal Imaging
Plastic components welded onto fuel tanks require precision to ensure structural soundness. Welder configurations make it challenging to gain visibility of component welds as they occur making inline inspection difficult.

Inline inspections of fuel tank component welds help teams greatly reduce the risk of shipping defective tanks compared to sample, destructive testing.
How Thermal Imaging Identifies Defects in Plastic Fuel Tank Component Welds
By deploying multiple thermal cameras, our solution helps teams capture images that are combined to generate a consistent view of the entire component weld area. By generating this consolidated view, our OneView inspection software creates a standardized digital perspective that can be used to train AI models to detect weld inconsistencies like cold spots that signal potential weaknesses.
By capturing and analyzing thermal profiles in real-time, Eigen’s AI solution enables manufacturers to ensure that each welded gas tank component meets high-quality standards.
This non-destructive inspection approach preserves components, reduces waste, and allows for a thorough, 100% inspection rate, setting a new standard for efficiency and accuracy in quality control.
Inspecting Shell Welds on Plastic Fuel Tanks
Shell welds are also critical for ensuring a plastic gas tank’s leak resistance. These welds must be precisely executed to withstand stress and maintain durability. Any inconsistency, such as insufficient bonding or gaps within the weld, could compromise the entire component, meaning inspecting shell welds on every tank is the best way to decrease the risk of shipping a tank with quality issues.
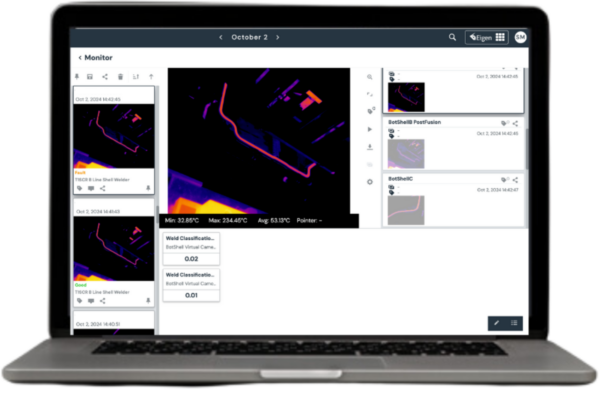
Digital, AI-powered inspection records give teams a “bird’s-eye” view of what happened in the welder during the weld. They can use those records to determine the cause of defects faster and make changes to the process to prevent reoccurrence.
Thermal Imaging and AI for Weld Quality Assurance
During the shell welding process, the heat distribution along the weld leg is an important indicator of weld quality. Eigen’s AI-powered thermal imaging captures this distribution in real-time, analyzing it to detect anomalies like uneven heating or weak bonds. Suppose any irregularities are detected, such as a cold spot, could suggest a gap or improper fusion. In that case, the solution flags the issue, allowing operators to take corrective action before the component moves further down the production line.
This early identification of potential issues not only ensures weld quality but also streamlines the manufacturing process, eliminating the need for post-production testing or manual inspection.
Key Benefits of AI-Powered Thermal Imaging for Weld Inspection
- Real-Time Defect Detection: By using thermal imaging, AI can analyze temperature profiles in the weld area in real-time. This identifies inconsistencies or potential weak points immediately.
- Non-Destructive Testing (NDT): Unlike traditional inspection methods, thermal imaging is non-invasive, allowing for the detection of hidden defects without touching or damaging the component.
- Enhanced Precision with Machine Learning: AI models can detect even subtle temperature anomalies that may indicate defects, leading to consistent and reliable inspections.
- Data-Driven Insights: Thermal data collected from weld inspections can be analyzed over time, helping manufacturers refine processes, improve quality control, and reduce waste.
Why Choose Eigen?
Along with years of expertise in AI-powered thermal imaging, we have a factory-proven tank weld inspection solution. It is deployed in more than 25 machines across 12 factories, delivering 10 million+ inspections per year. It provides teams with real-time, non-destructive inspection and traceable inspection records for every tank.
Our AI-driven technology doesn’t just detect defects—it continuously gathers data across production runs, allowing factory teams to refine and improve their weld processes over time. By providing image-based documentation and traceability, Eigen’s solutions also help manufacturers build a reliable quality history for each tank, offering confidence in product integrity and compliance with industry standards.
Key Advantages of Choosing Eigen:
- Precision and Accuracy: Detects “invisible” anomalies, ensuring each weld meets strict quality standards.
- 100% Inspection Coverage & Traceability: Enables inspection of every weld without slowing down production and generates a traceable digital inspection record.
- Sustainability and Efficiency: Reduces waste and minimizes energy consumption by preventing defects from moving further down the line.
Moving Forward: Elevating Quality Assurance in the Automotive Industry
In an industry where safety, efficiency, and sustainability are paramount, AI-powered thermal imaging inspections provide next-level quality assurance. By partnering with Eigen, tank manufacturers can adopt a forward-thinking approach to inspection that reduces waste, increases efficiency, and ensures every component meets the highest standards.
Contact us today to discuss how we can help your team move your fuel tank weld inspections inline with our AI-driven thermal inspection solution.