Manufacturers looking to add AI-enabled quality inspections to ensure product quality and maintain efficiency have a lot of choices when it comes to solutions. While there have been amazing advancements in camera technology and software, many solution providers continue to offer status quo camera-based systems – stand-alone solutions that detect issues based on images alone.
Raw images do not deliver the best inspections because of “noise”, varying environmental conditions (lighting) and variations in product position/placement. To overcome these challenges, we developed novel image processing and enhancement capabilities. The standardized images our software generates make training inspection models easier. While our inspection images can show you the “what” they do not tell you the “why”. Quality and Production teams need to know that a product has a defect AND what has caused it. Our OneView software merges process data with our inspection images giving factory teams the data and tools to determine the “why”.
Our ability to help teams immediately connect the dots between quality issues and their cause is one of the key ways Eigen stands out amongst machine vision inspection solutions providers. Here are a few more things that make us unique in the inline inspection market.
1. High-Resolution Thermal Imaging
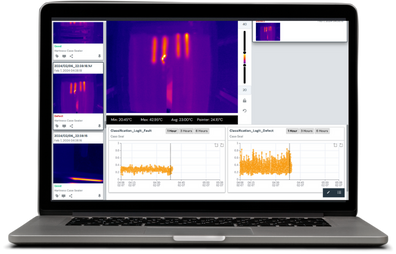
Thermography – thermal imaging – is under utilized in quality inspections in manufacturing. We’re unlocking it’s full potentiall and helping manufacturers adopt thermal inspection solutions at scale.
Many of our turnkey solutions include high-resolution thermal imaging, a technology that is still relatively uncommon in many factories. Thermal imaging can detect “invisible” anomalies that can’t be seen with the human eye or traditional cameras. By capturing temperature variations with high precision, our solutions can identify defects related to material inconsistencies, structural weaknesses, and other subtle issues that might otherwise go unnoticed. This capability is particularly beneficial in industries where material integrity is critical, such as plastic and metal parts for automotive manufacturing.
2. Advanced AI and Machine Learning Capabilities
Another differentiator is our robust use of artificial intelligence (AI) and machine learning (ML). While many companies incorporate basic AI, Eigen goes one step further, helping factory teams build sophisticated algorithms that continuously learn and adapt. This dynamic approach allows our solutions to improve accuracy over time, reducing false positives and enhancing defect detection capabilities. The result is a solution that identifies issues AND predicts and prevents future defects, leading to significant cost savings and improved product quality.
3. Seamless Integration and Scalability
Implementing new technology often comes with the challenge of integration. As mentioned above, many factory machine vision inspection systems are not connected to machines, PLCs and other sensors. An image from a camera only tells part of each product’s quality story. Comprehensive inline inspections can only happen when data is captured and shared from all these sources. All of our solutions integrate with existing manufacturing systems. They are highly compatible with various equipment and software, ensuring a smooth transition without disrupting production. The solution configuration (cameras used, data connectivity and networking) can be transferred to other machines. For our customers this means quickly expanding and standardizing inspections – all centrally managed with OneView.
4. Real-Time Data Analytics and Reporting
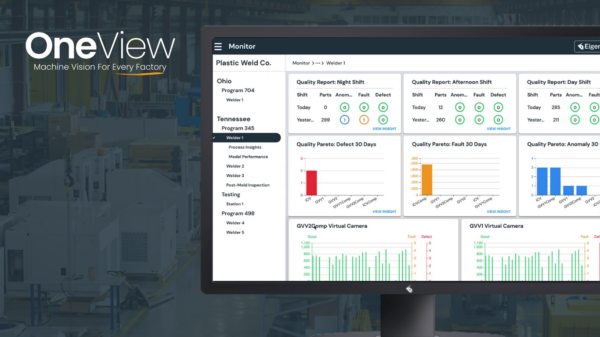
Many of our customers now start their shifts here – reviewing summaries of the inspections from the previous day or shift and determining what needs their immediate attention.
We mentioned this above but it merritts repeating. In today’s data-driven world, having access to real-time analytics is crucial. Our software provides comprehensive data analysis and reporting tools. OneView offers detailed insights into production processes, enabling manufacturers to make informed decisions quickly. Real-time data helps identify trends, optimize processes, and implement corrective actions immediately, reducing downtime and improving overall efficiency. This level of transparency and immediacy is something that status quo solutions lack and significantly benefits our customers.
5. Strong Industry Knowledge, Partnerships and Customer Support
Eigen understands that technology alone isn’t enough; strong partnerships and support are essential for success. Our company has established collaborations with industry leaders and research institutions, fostering innovation and staying ahead of technological advancements. Moreover, we are committed to providing exceptional customer support. We focus exclusively on manufacturing and our team includes engineers with extensive experience and domain knowledge. Our team works closely with customers to ensure the solutions are tailored to their specific needs, offering training and ongoing assistance to maximize the benefits of their technology.
Benefits Beyond the Tangibles
Our solutions deliver clear and proven tangible benefits including reduced scrap, downtime and process optimization. Beyond these tangible results, we are giving Production and Quality teams confidence in the quality of every part and security in knowing that they have a standardized, comprehensive digital inspection of every part they produce. They no longer have to rely on highly-subjective, sample testing or worry about time-consuming investigations. They can avoid wasting money destroying good products for testing. Eigen stands out among providers offering inline quality inspection solutions for manufacturing in delivering all of these tangible and intangible benefits every time.
To learn how our company and our integrated, inline non-destructive inspection solutions, drop us a line.