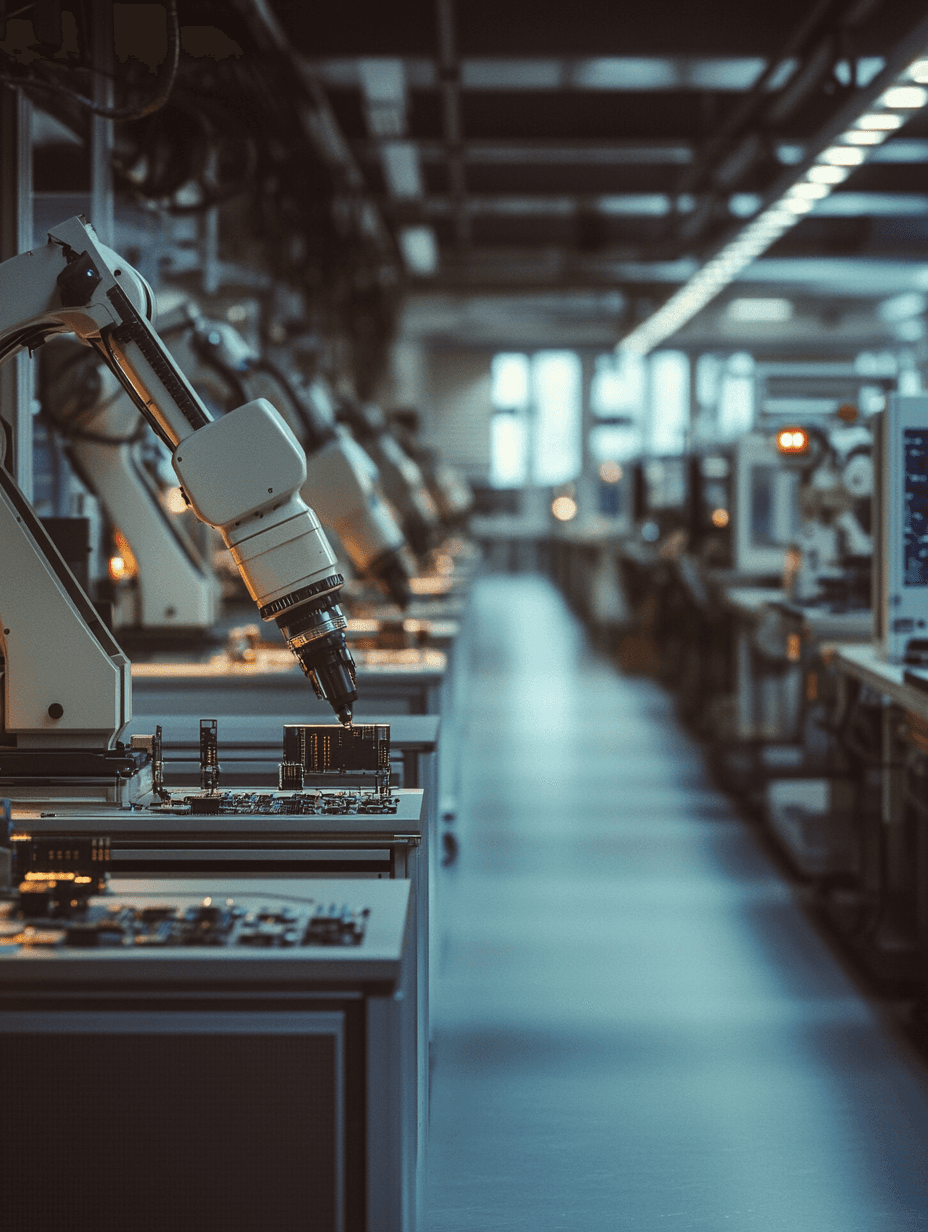
AI Powered Vision
Seeing Beyond Defects
AI Powered Vision
Seeing Beyond Defects
Eigen combines imaging and AI to detect issues traditional vision systems miss, revolutionizing quality inspection.
Eigen combines imaging and AI to detect issues traditional vision systems miss, revolutionizing quality inspection.
AI Vision Today
How Eigen Solves for It
How We’re Different
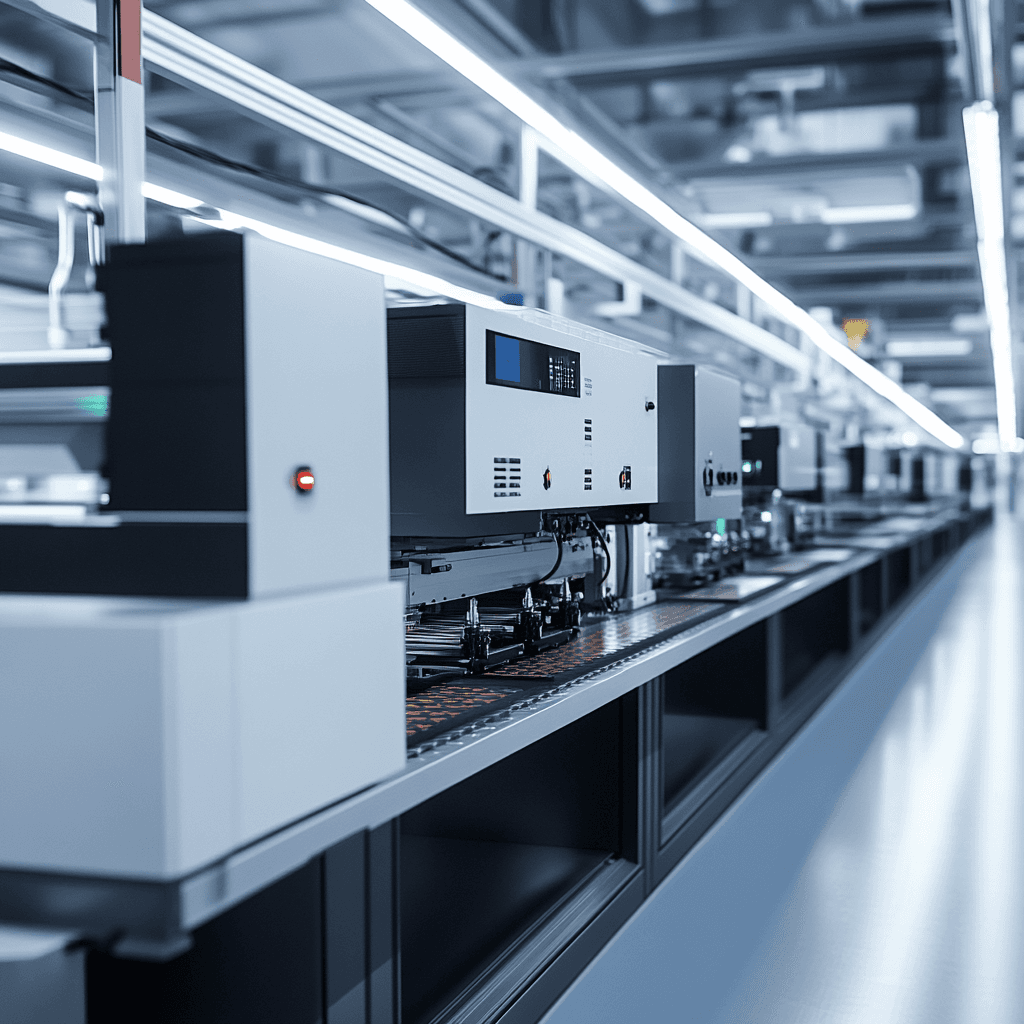
Expert Dependence
AI vision solutions require specialized data science teams to implement and maintain.
Scalability Barrier
Solutions force manufacturers to choose application-specific tools that don't scale.
Workflow Gaps
Solutions force manufacturers to choose generic platforms missing critical workflow components.
Delayed Returns
The time required to achieve ROI can be extensive.
AI Vision Today
How Eigen Solves for It
How We’re Different
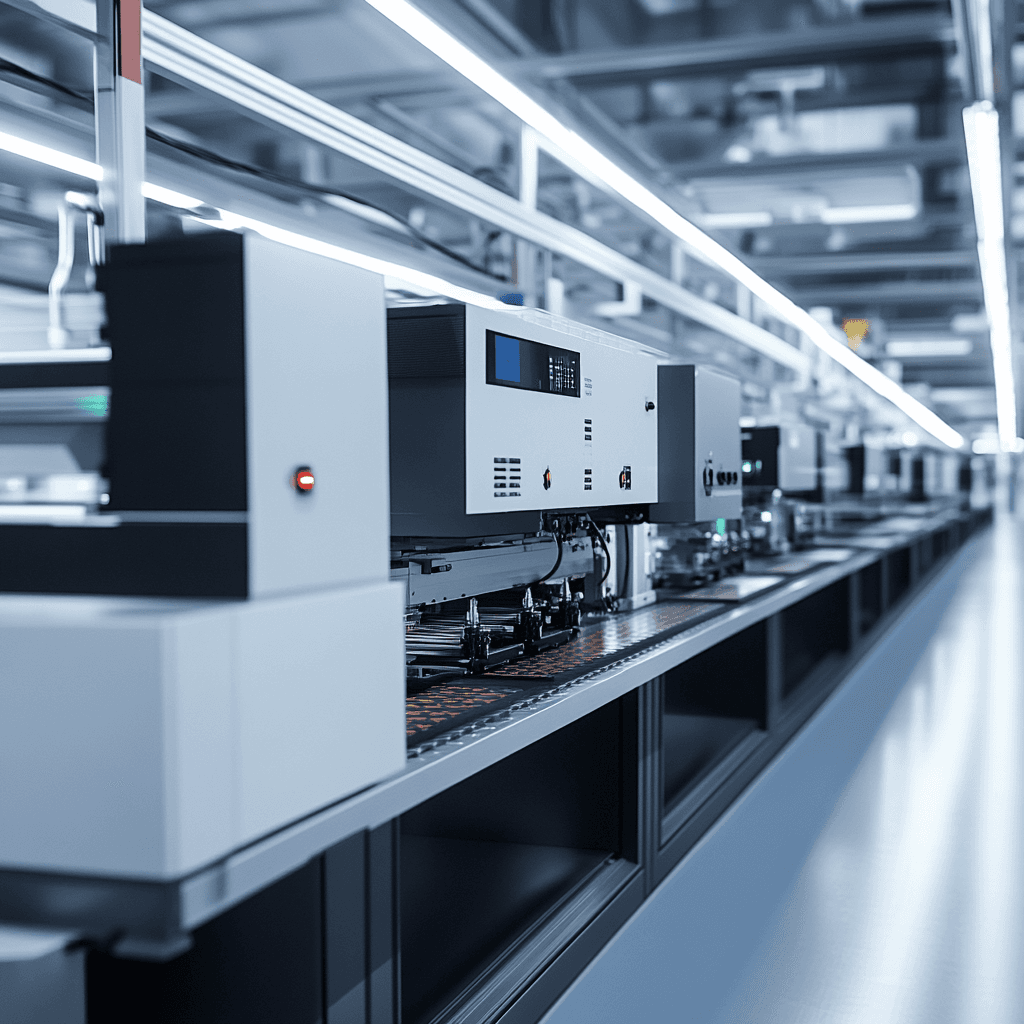
Expert Dependence
AI vision solutions require specialized data science teams to implement and maintain.
Scalability Barrier
Solutions force manufacturers to choose application-specific tools that don't scale.
Workflow Gaps
Solutions force manufacturers to choose generic platforms missing critical workflow components.
Delayed Returns
The time required to achieve ROI can be extensive.
AI Vision Today
How Eigen Solves for It
How We’re Different
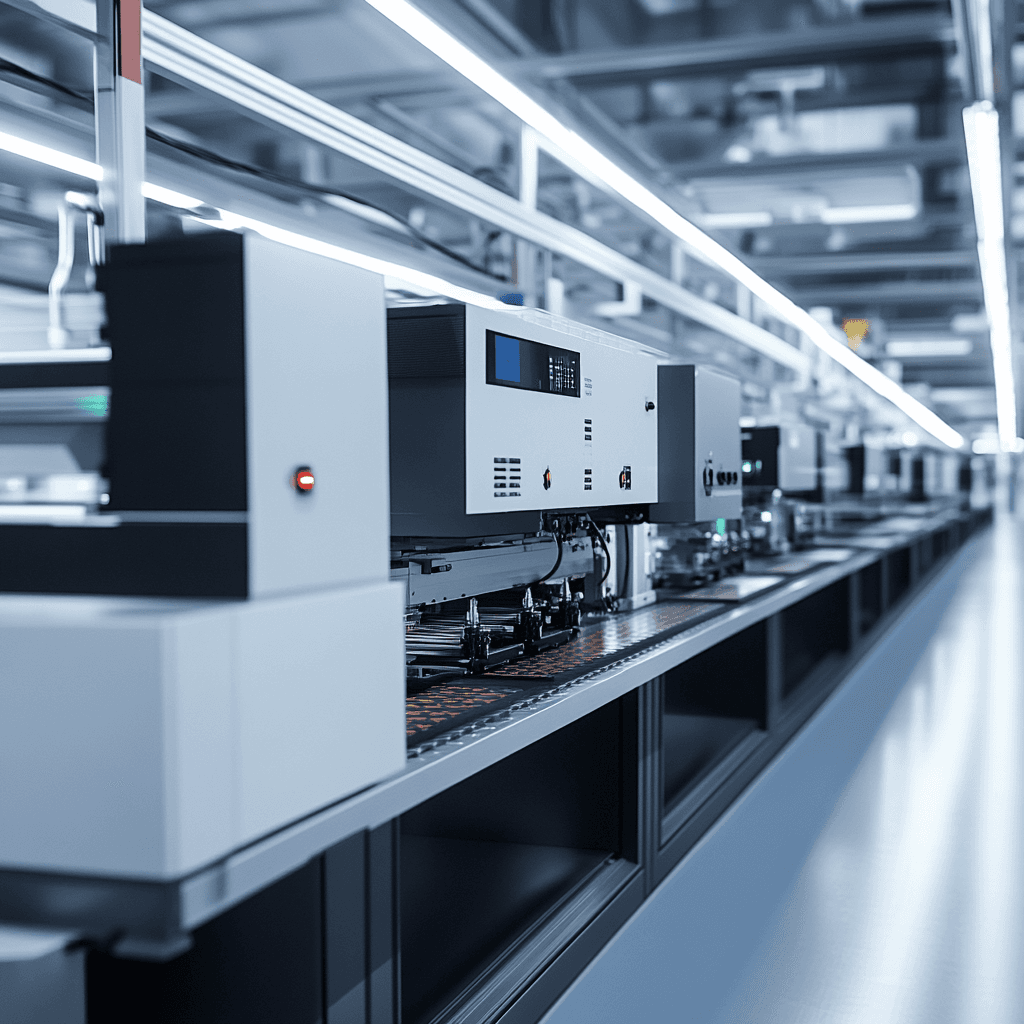
Expert Dependence
AI vision solutions require specialized data science teams to implement and maintain.
Scalability Barrier
Solutions force manufacturers to choose application-specific tools that don't scale.
Workflow Gaps
Solutions force manufacturers to choose generic platforms missing critical workflow components.
Delayed Returns
The time required to achieve ROI can be extensive.
Over
2.5 Billion
Quality Metrics Analysed
Over
1 Billion
Images Processsed Daily
Over
180,000
Events Monitored Daily
Over
29,000
Parts Verified Everyday
Over
2.5 Billion
Quality Metrics Analysed
Over
1 Billion
Images Processsed Daily
Over
180,000
Events Monitored Daily
Over
29,000
Parts Verified Everyday
Over
2.5 Billion
Quality Metrics Analysed
Over
1 Billion
Images Processsed Daily
Over
180,000
Events Monitored Daily
Over
29,000
Parts Verified Everyday

OneView eliminates tradeoffs in vision AI implementation, providing a complete end-to-end platform for design, deployment, monitoring, and management—requiring no specialized expertise while transforming a high-risk, high-cost initiative into a scalable, value-driven solution.
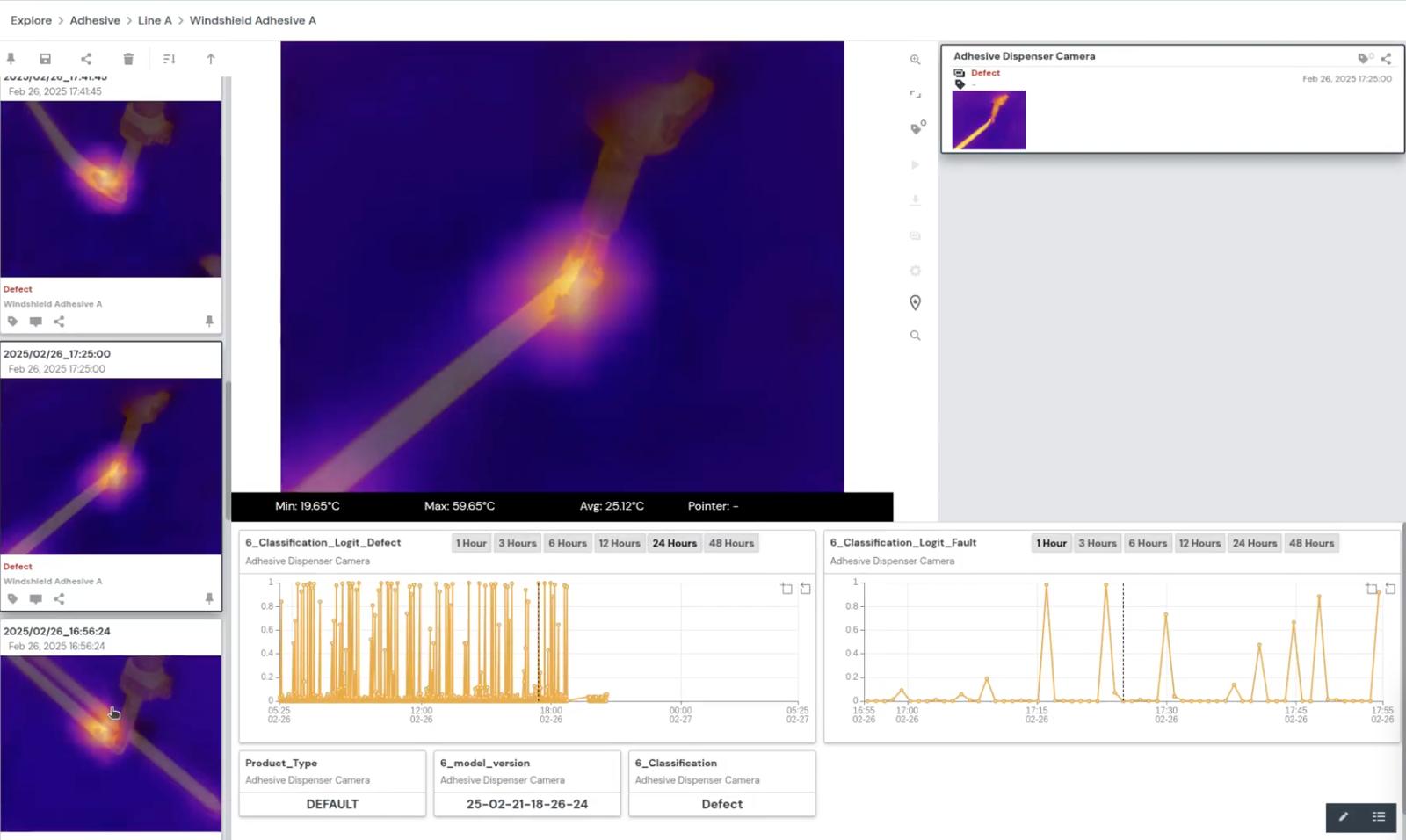
Key Features:
Anomaly Detection
No-Code AI Model Training
Prediction Heatmaps
Image / Data Ingestion
Data Consolidation & Searchability
Automated Quality & Anomaly Reports
Find & Contain Similar Defects
Explainable AI Predictions

OneView eliminates tradeoffs in vision AI implementation, providing a complete end-to-end platform for design, deployment, monitoring, and management—requiring no specialized expertise while transforming a high-risk, high-cost initiative into a scalable, value-driven solution.
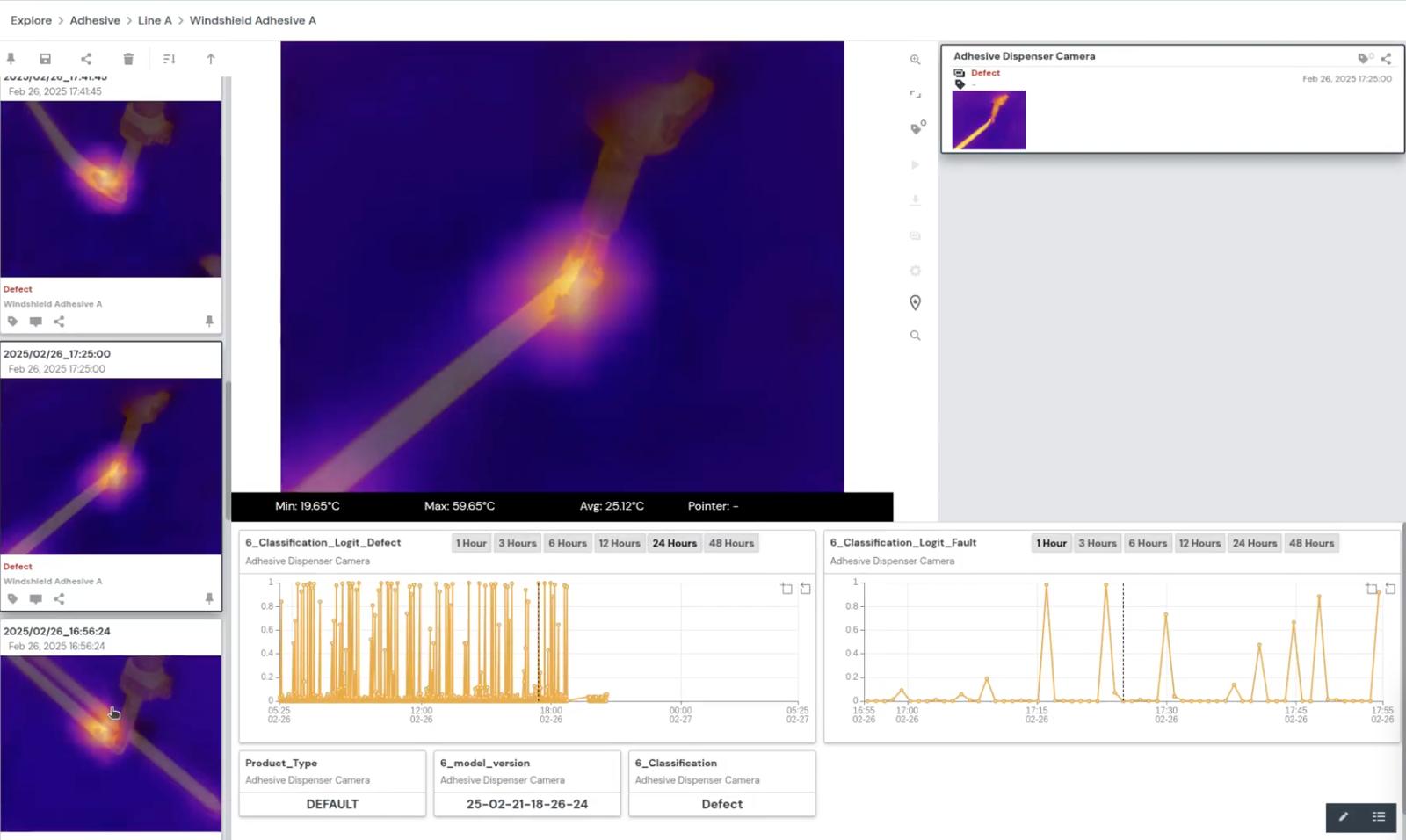
Key Features:
Anomaly Detection
No-Code AI Model Training
Prediction Heatmaps
Image / Data Ingestion
Data Consolidation & Searchability
Automated Quality & Anomaly Reports
Find & Contain Similar Defects
Explainable AI Predictions

OneView eliminates tradeoffs in vision AI implementation, providing a complete end-to-end platform for design, deployment, monitoring, and management—requiring no specialized expertise while transforming a high-risk, high-cost initiative into a scalable, value-driven solution.
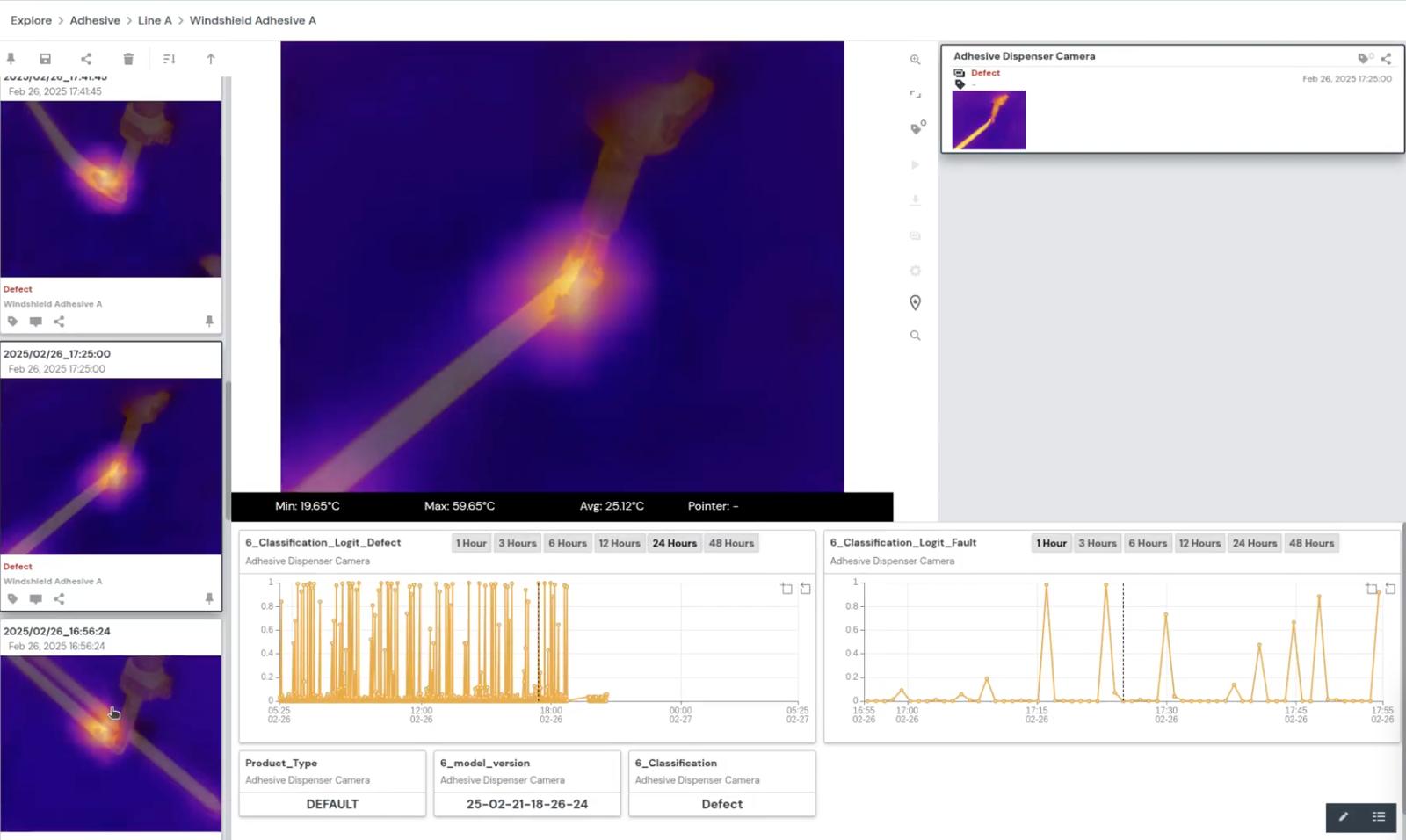
Key Features:
Anomaly Detection
No-Code AI Model Training
Prediction Heatmaps
Image / Data Ingestion
Data Consolidation & Searchability
Automated Quality & Anomaly Reports
Find & Contain Similar Defects
Explainable AI Predictions
Thermal Vision Applications
Thermal Vision Applications
Eigen specializes in combining thermal imaging with advanced AI to detect issues that traditional systems miss, enabling a new era of quality inspection for heat-critical manufacturing processes
Eigen specializes in combining thermal imaging with advanced AI to detect issues that traditional systems miss, enabling a new era of quality inspection for heat-critical manufacturing processes
[4]
[3]
[2]
[1]
[5]
Adhesive
Application
Drywall
Manufacturing
Speciality Paper
Manufacturing
Metal
Welding
Plastic
Welding
Packaging
& Adhesives
Metals
Plastics
Building
Materials
[4]
[3]
[2]
[1]
[5]
[4]
[3]
[2]
[1]
[5]
[4]
[3]
[2]
[1]
[5]
[4]
[3]
[2]
[1]
[5]
[4]
[3]
[2]
[1]
[5]
Problem Manufacturers rely on sample destructive testing to ensure weld integrity. Solution Thermal cameras capture multiple views of the weld process, and our AI predicts weld quality in real-time.
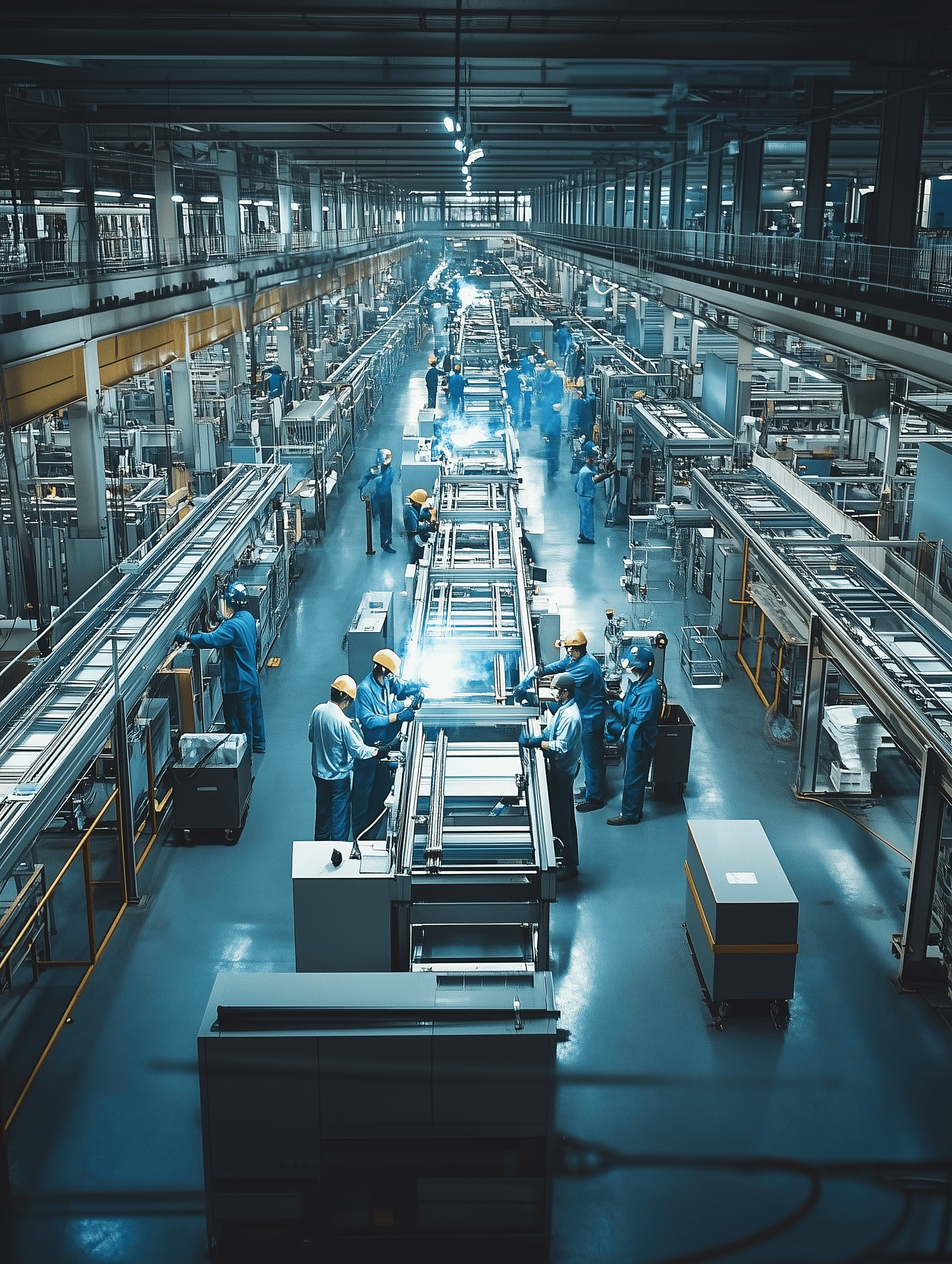
[4]
[3]
[2]
[1]
[5]
Adhesive
Application
Drywall
Manufacturing
Speciality Paper
Manufacturing
Metal
Welding
Plastic
Welding
Packaging
& Adhesives
Metals
Plastics
Building
Materials
[4]
[3]
[2]
[1]
[5]
[4]
[3]
[2]
[1]
[5]
[4]
[3]
[2]
[1]
[5]
[4]
[3]
[2]
[1]
[5]
[4]
[3]
[2]
[1]
[5]
Problem Manufacturers rely on sample destructive testing to ensure weld integrity. Solution Thermal cameras capture multiple views of the weld process, and our AI predicts weld quality in real-time.
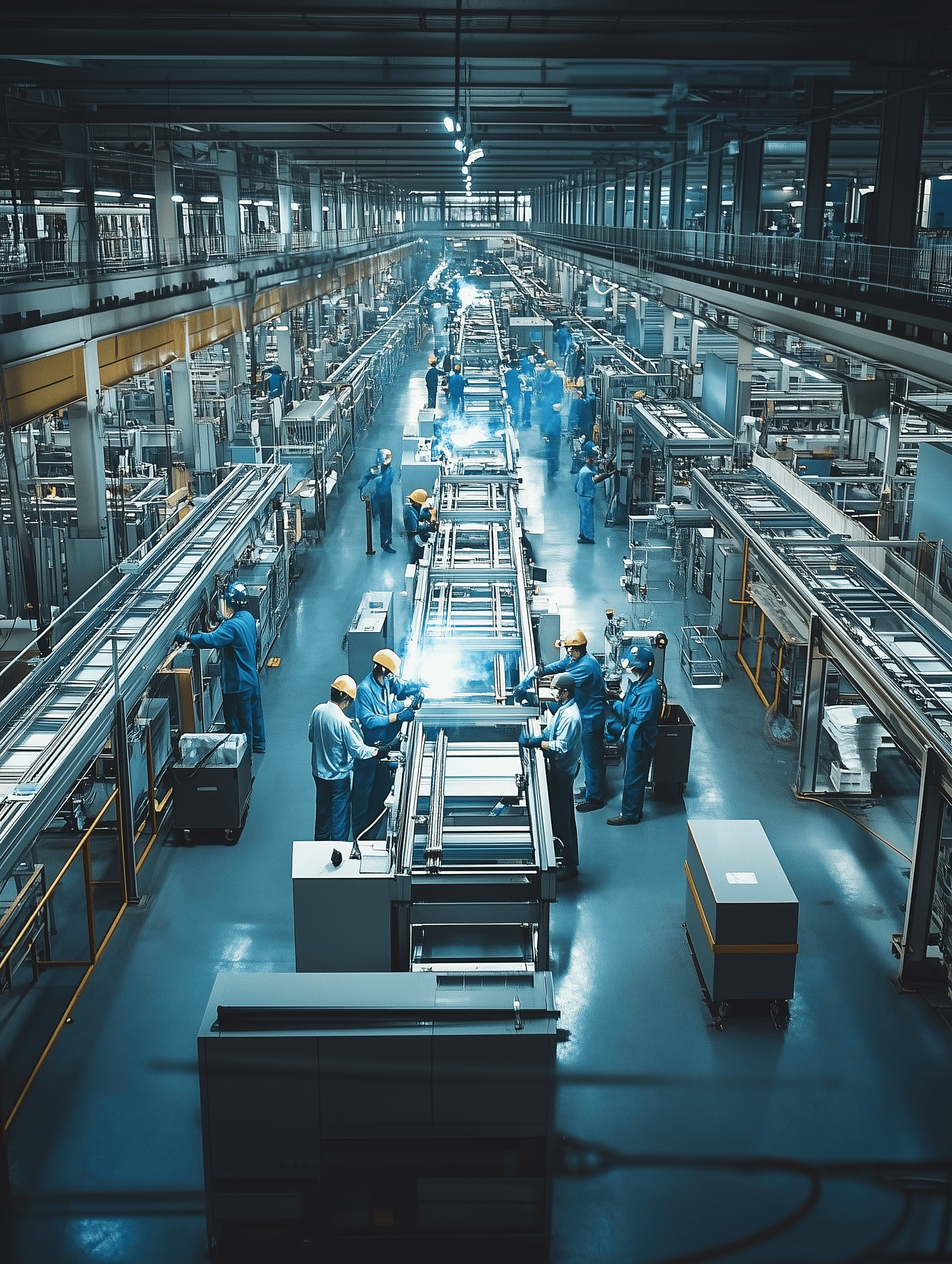
[4]
[3]
[2]
[1]
[5]
Adhesive
Application
Drywall
Manufacturing
Speciality Paper
Manufacturing
Metal
Welding
Plastic
Welding
Packaging
& Adhesives
Metals
Plastics
Building
Materials
[4]
[3]
[2]
[1]
[5]
[4]
[3]
[2]
[1]
[5]
[4]
[3]
[2]
[1]
[5]
[4]
[3]
[2]
[1]
[5]
[4]
[3]
[2]
[1]
[5]
Problem Manufacturers rely on sample destructive testing to ensure weld integrity. Solution Thermal cameras capture multiple views of the weld process, and our AI predicts weld quality in real-time.
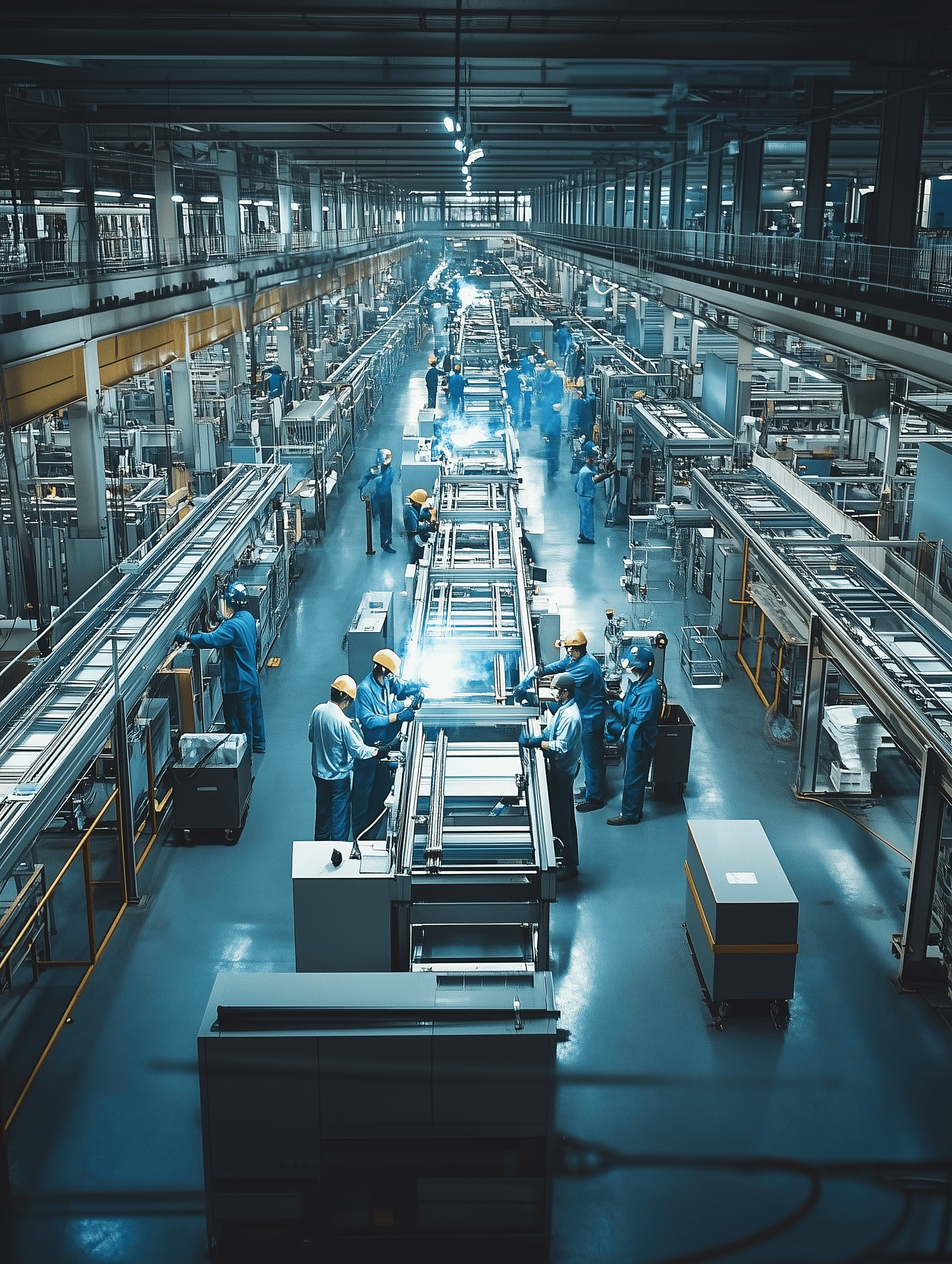
Explore
Case Studies
Explore
Case Studies
Get Started Today!
Get started with Eigen OneView | Cloud
Now available for a free trial - Book Today.
Get started with Eigen OneView | Cloud
Now available for a free trial - Book Today.
Trusted By Industry Leaders
Trusted By Leaders