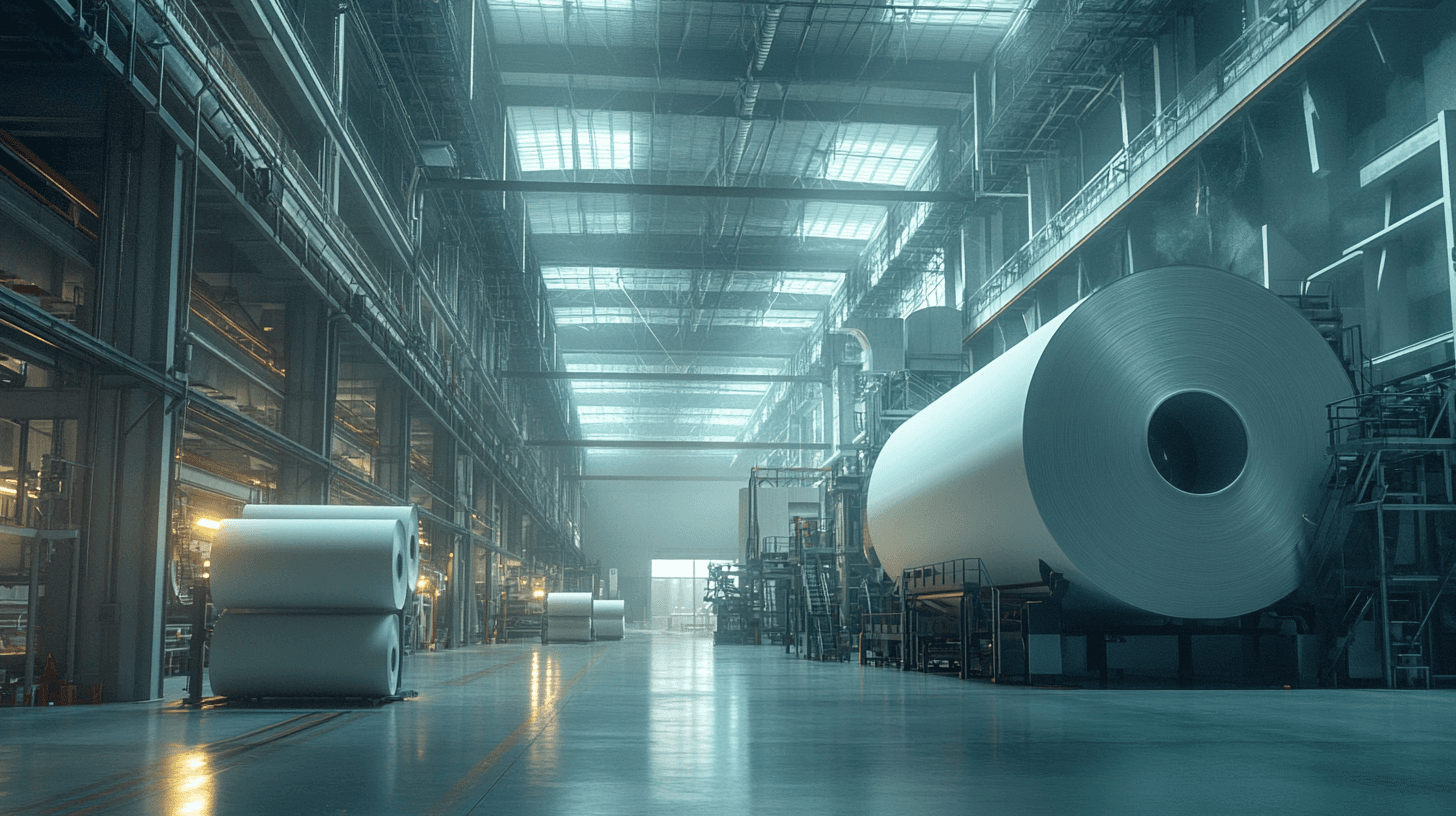
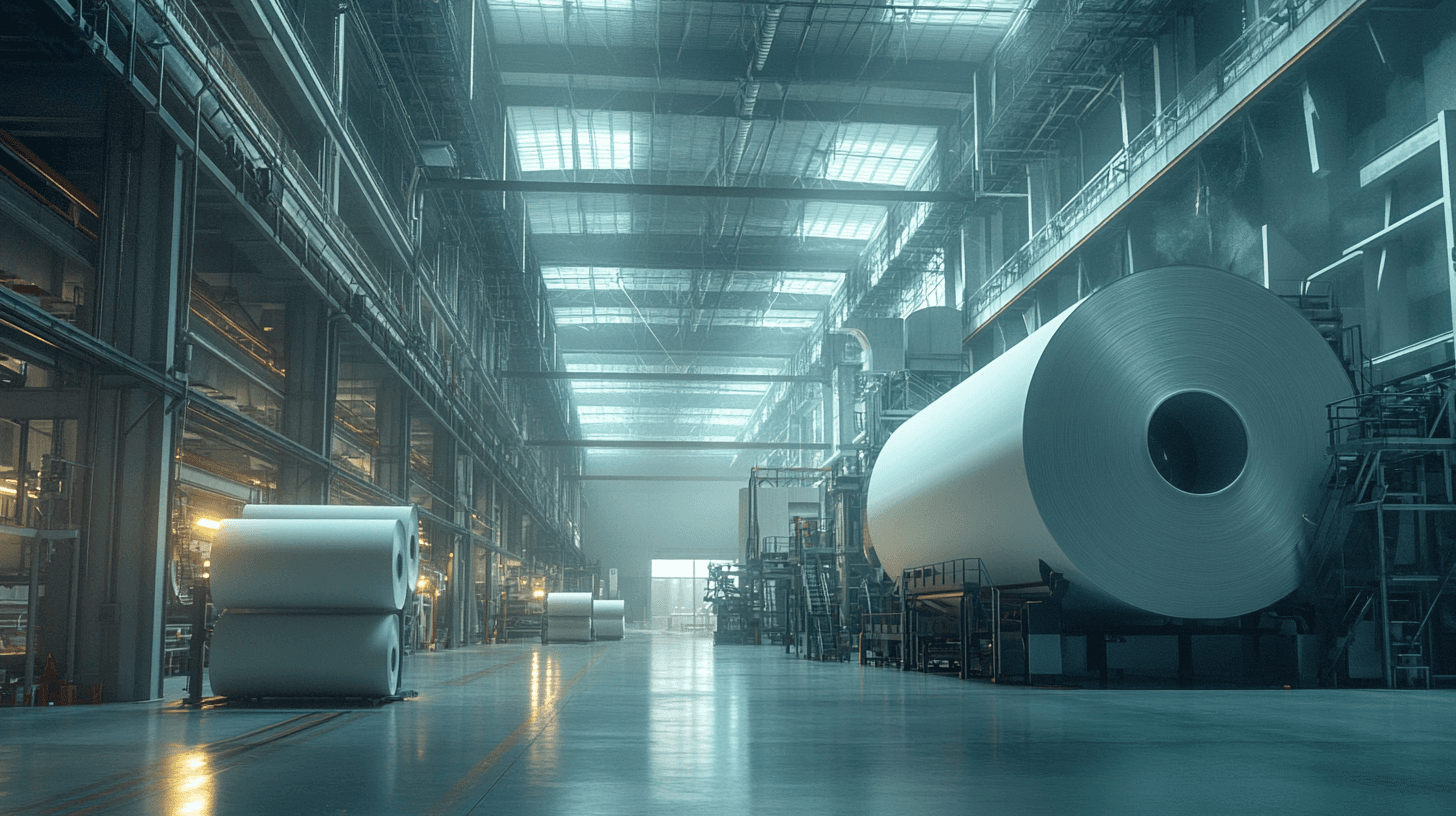
Case Study
Industry
Headquarters
Employees
Sappi - Speciality Paper Inspection
Sappi - Speciality Paper Inspection
TAGS
Paper and Packaging
Thermal Inspection
Industry
Pulp & Paper
Headquarters
South Africa
Employees
12,500
Company Profile
Sappi is a global diversified woodfiber company focused on providing dissolving pulp, specialty and packaging papers, printing and writing papers, as well as biomaterials and biochemicals to our direct and indirect customer base across more than 150 countries. The company produces approximately 5.7 million tons of paper per year.
Sappi is a global diversified woodfiber company focused on providing dissolving pulp, specialty and packaging papers, printing and writing papers, as well as biomaterials and biochemicals to our direct and indirect customer base across more than 150 countries. The company produces approximately 5.7 million tons of paper per year.
Challenge
Sappi was incurring quality-related costs due to downtime and equipment damage on its specialty papers lines. Rapid coating build-up during production was causing quality issues (streaks) and an optical machine vision solution was unable to detect the moisture changes in time to take preventive action.
Sappi was incurring quality-related costs due to downtime and equipment damage on its specialty papers lines. Rapid coating build-up during production was causing quality issues (streaks) and an optical machine vision solution was unable to detect the moisture changes in time to take preventive action.
Solution
The Eigen team designed a vision solution featuring thermal cameras which could detect the temperature variation that indicated streaks and coating build-up.
Monitors in the factory alert operators when potential issues are detected. Along with using Eigen’s OneView software for real-time monitoring, the production and quality teams have interlocked the solution – automatically unloaded the calendars when significant build-up events are detected.
The Eigen team designed a vision solution featuring thermal cameras which could detect the temperature variation that indicated streaks and coating build-up.
Monitors in the factory alert operators when potential issues are detected. Along with using Eigen’s OneView software for real-time monitoring, the production and quality teams have interlocked the solution – automatically unloaded the calendars when significant build-up events are detected.
Impact
Real-Time Streak Monitoring
Reduced Downtime
Closed-Loop Automation
Standardized Data & Records
$1M+ Savings Across 3 Factories
Real-Time Streak Monitoring
Reduced Downtime
Closed-Loop Automation
Standardized Data & Records
$1M+ Savings Across 3 Factories